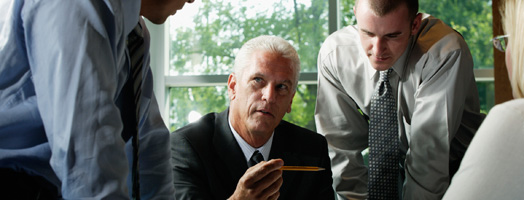
Critical Chain Case Study
About OMRON
Since its establishment in 1976, OMRON SOFTWARE Co., Ltd has developed public systems, or more appropriately, social infrastructures. For over 30 years these have included such projects as urban traffic control systems, train station automation systems, financial ATMs, and credit card point-of-sale systems.
The Challenge
OMRON had embarked on the development of small to medium scale system and was working with a partner company. OMRON recognized an issue with the delivery date and wondered, "Is it really OK when the person in charge assures you 'OK'?" When leaders asked about progress, the project leader reported back, "We're doing alright." However, what was actually meant was, "We're doing our best to meet the deadline."
Fearing a delivery delay, OMRON decided to introduce critical chain project management with Being Management 3 software for this initiative.
How Critical Chain Helped OMRON's Business
The development of the "ene-brain," an energy-saving auto-analysis system of OMRON's Environmental Division, was at a critical point. Severe price competition and other internal factors result in a strict requirement for "shortest leadtime and lowest cost" for all projects at OMRON.
Flash back to 2009, just three days before the delivery date of another important development project, the project manager discovered that, "It's not possible to make it in time." In only three days, nothing can be done. As a result, the important project was delivered late.
This time, the project manager decided to use critical chain project management to prevent a delivery delay and, since there are many different projects for the limited number of staff (one person might work on 5 or more projects simultaneously), it also helped to check the resource balance and multitasking.
The Team's Experience With Critical Chain
Right away, the project team using critical chain noticed a big difference in the environment they were working in. Listed below are the team's feedback on their experience before and after critical chain was implemented.
Before | After |
It was almost impossible to determine the actual progress and occasionally the scope of the project could not be properly managed. | Due to the simple management system, every day the progress status was easily entered and reported. |
It was difficult to spot a delay until very close to the deadline. | It is all clear how much buffer is available before the delivery date, and issues were easily handled with early countermeasures. |
There were some projects that failed to meet the delivery date. | After CCPM was introduced, all projects have been completed on time.
|
It was very difficult to identify when resources were overloaded. | It has become very easy to check resources on the critical chain and make resource assignments. |
Project progress status was not fully understood and it was difficult to judge if it was feasible to schedule additional tasks. | Resource load status is easily determined and it is now possible to know when to start an additional task or request other team members to switch tasks to deal with delays and changes in the project. |